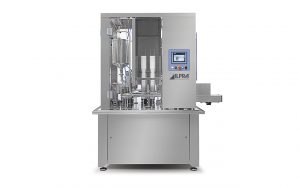
Rotative
Fill Seal 5000
Full Description
The Fill Seal 5000 stands out as the most sought-after pot filler machine in the dairy packaging industry, thanks to its ultra-compact design and wide range of optional features.
This automatic filling and sealing machine is capable of handling MAP (Modified Atmosphere Packaging), vacuum sealing, and gas flushing, offering a versatile solution to extend the shelf life of dairy products and maintain their freshness. The machine’s control panel allows for straightforward operation, with the ability to store several recipes for quick setup changes, enhancing productivity and flexibility in production lines.
Equipped to work with pots of different materials, the Fill Seal 5000 can process two cups per cycle, with configurations available for both standard and large sizes, accommodating various cup dimensions and volumes. Its technical specifications highlight its adaptability and efficiency, with options for different electric power settings, pot sizes, and maximum cup heights to suit a broad range of packaging needs.
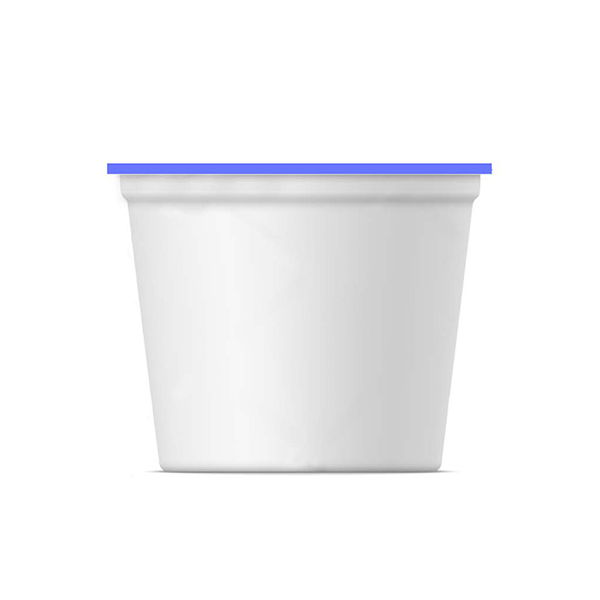
- Sealing -
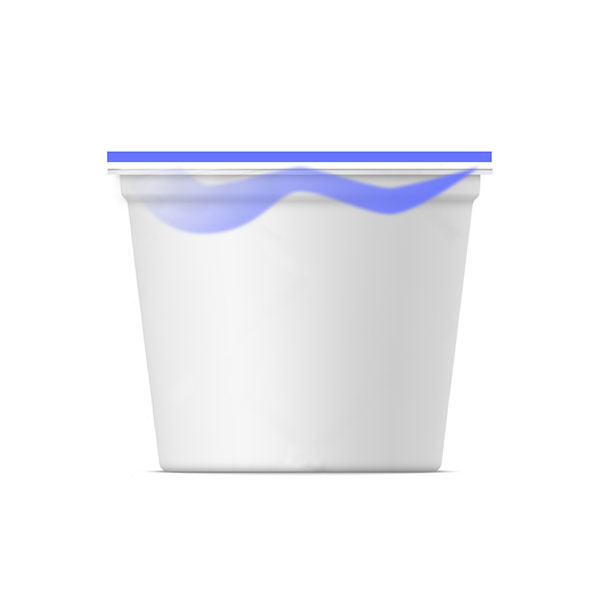
- Gas Flush -
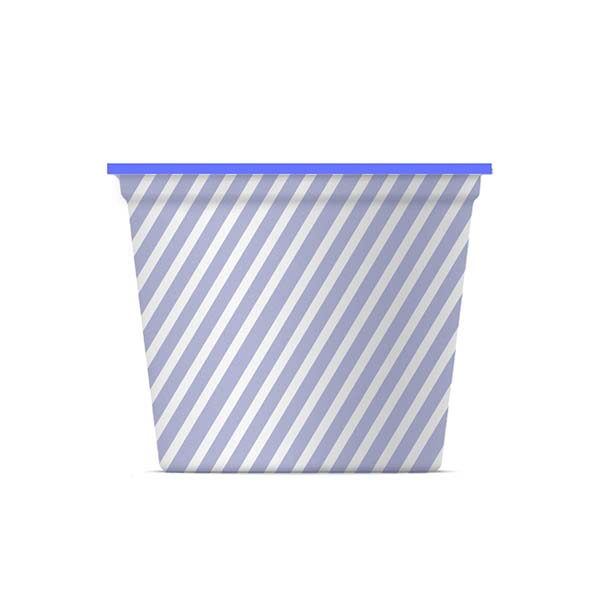
- MAP/ATP -
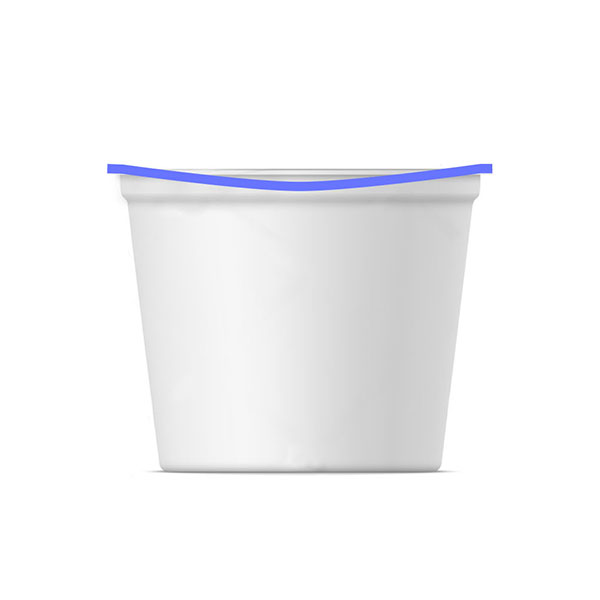
- Vacuum -
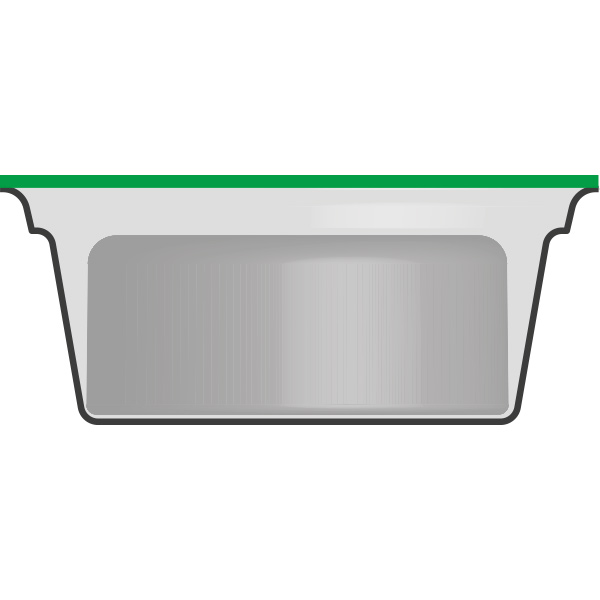
Sealing
Up to 40 cpm
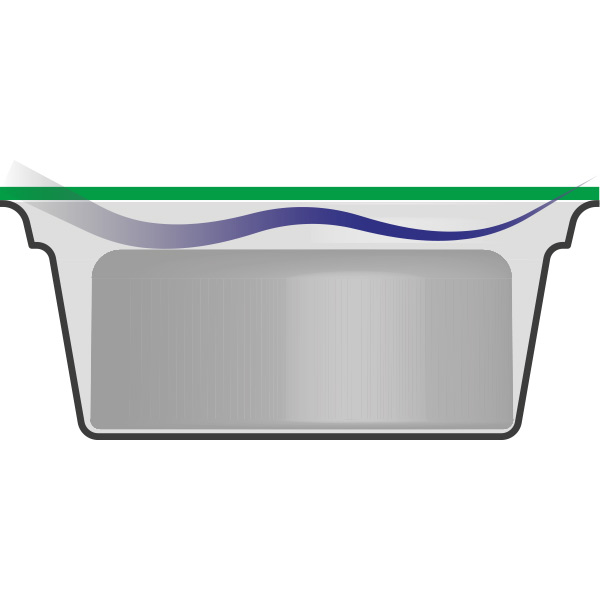
Gas Flush
Up to 30 cpm
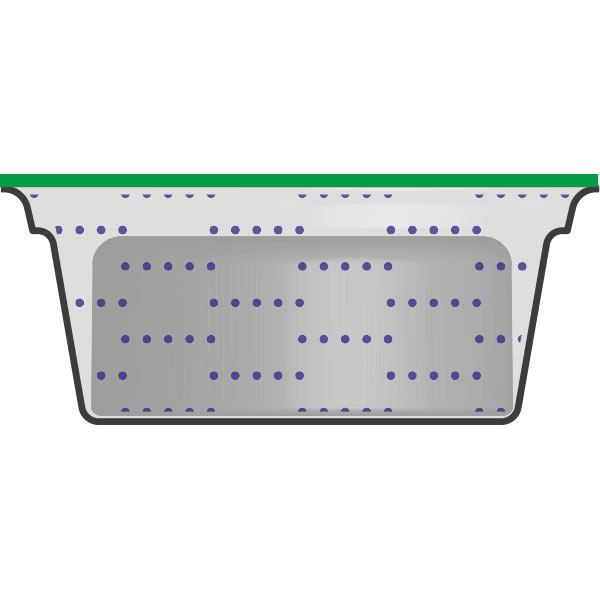
MAP/ATP
Up to 20 cpm
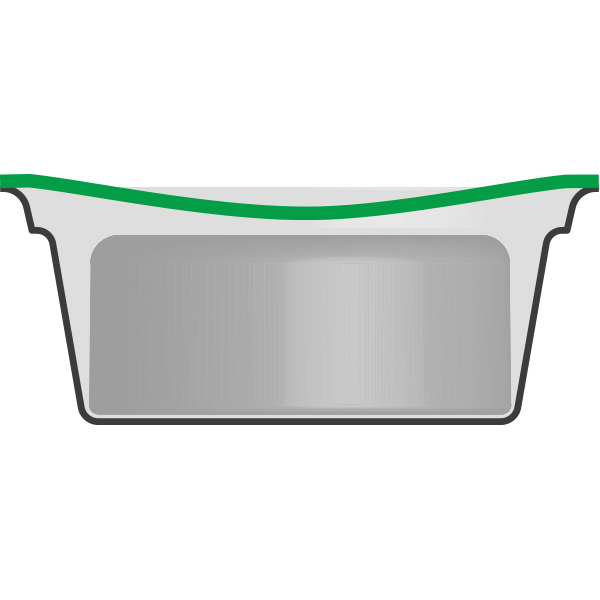
Vacuum
Up to 32 cpm
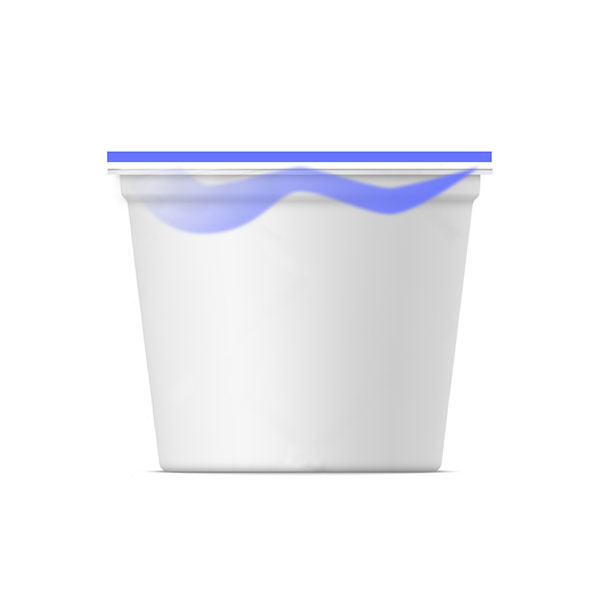
Gas Flush Fill
Up to 30 cpm
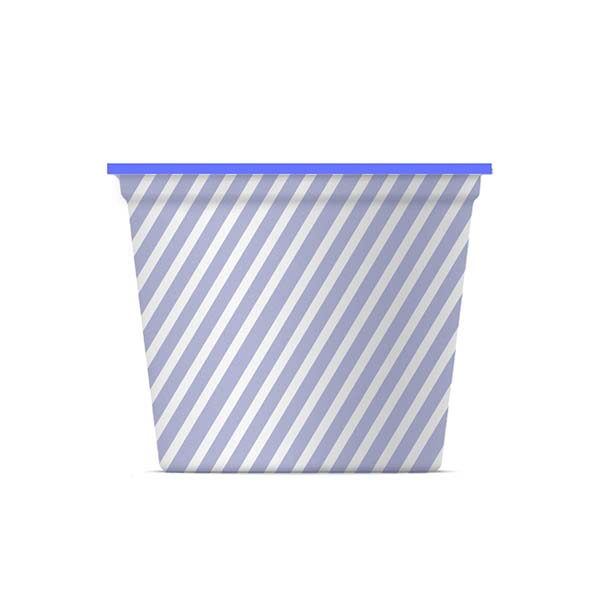
MAP/ATP Fill
Up to 20 cpm
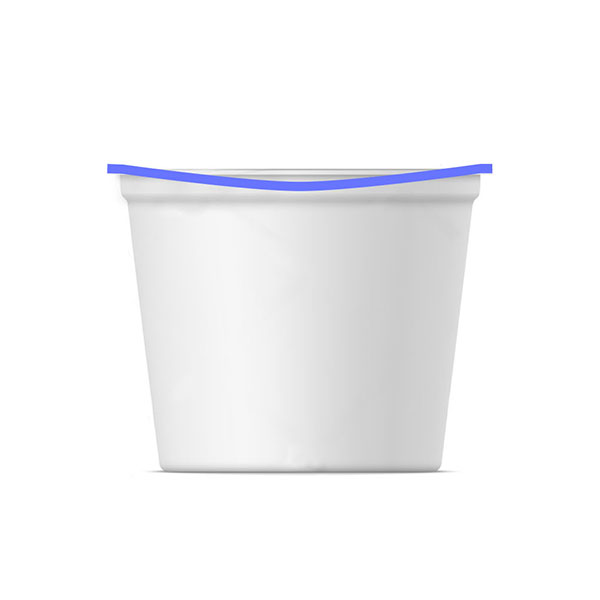
Vacuum Fill
Up to 32 cpm
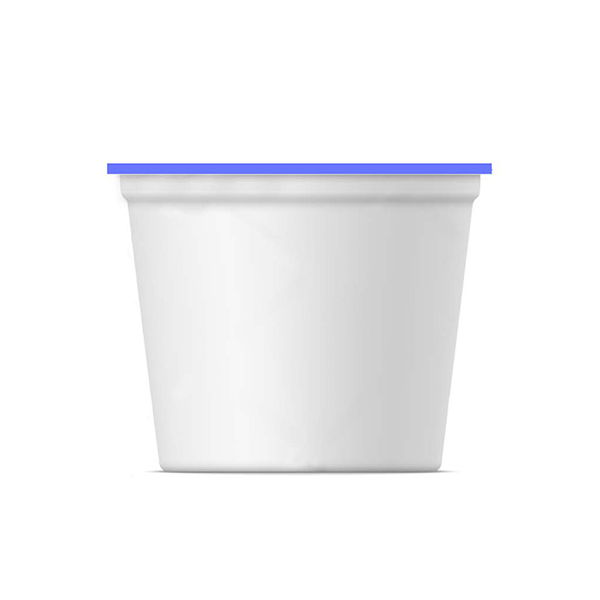
Sealing Fill
Up to 40 cpm
Technical Data
Technical data : Fill Seal 5000>
Dimensions : 172 x 169 x h 198 cm >
Weight: circa 850 Kg >
Electric Power Lid: 4,5 Kw >
Electric Power Film: - >
Pots per cycle: 2>
Ø Max Cups Lid: 95 mm >
Ø Max Cups Film : 90 mm>
Max height Cup: 170 mm>
Technical data : Fill Seal 5000 Large>
Dimensions : 154 x 220 x h 232 cm (Lid)>
Weight: circa 1050 Kg >
Electric Power Lid: 7,5 Kw >
Electric Power Film: 7 (N) - 8,5 (VG) kW>
Pots per cycle: 2>
Ø Max Cups Lid: 130 mm >
Ø Max Cups Film : 120 mm (N ) >
Max height Cup: 130 mm>
Dimensions : 215 x 193 x h 232 cm (Film)>
Ø Max Cups Film : 105 (VG)>
Videos
Layered Dessert Pots
Split Cup Yogurt Pots
Layered Yogurt in Glass Jars
Technology
High-Capacity Storage
Designed to maximise operational efficiency, the high-capacity storage feature of the Fill Seal 5000 reduces the need for frequent refills, ensuring that the machine and its operators can maintain high levels of productivity with greater autonomy.
Pick & Place
The automatic pick & place device is a critical component for enhancing the machine’s automation capabilities. It seamlessly integrates into the production line to accurately place pre-filled containers into the machine, reducing manual handling and improving overall efficiency.
Suction of Foreign Materials
Ensuring product purity is essential, and the suction of foreign materials accessory addresses this by removing any contaminants from the containers. An air jet strategically placed near the container’s bottom lifts and extracts foreign bodies, maintaining the integrity of the packaged product.
Ultra Cleaning System
The ultra cleaning system accessory equips the Fill Seal 5000 with advanced sanitisation capabilities, including UVC lamps, pulsed light, and hydrogen peroxide options. This system is essential for maintaining a sterile production environment, crucial for food safety.
Dosing Systems
With a comprehensive range of dosing systems available, the Fill Seal 5000 can achieve fast and accurate filling for various products. Whether dealing with liquids, creams, or granular materials, these dosing systems ensure precise product volumes are dispensed every time.
Laminar Flow Hood
The laminar flow hood creates a controlled environment by providing a constant flow of micro-filtered air over the production area. This feature is instrumental in extending the shelf life of products by protecting them from airborne contaminants during the packaging process.
Crimping System
The crimping system accessory is designed for the secure sealing of lids onto glass or ceramic pots. By crimping the lid to the pot’s side edge, it ensures a tight seal, preserving the product’s quality and safety throughout its shelf life.
Inkjet
The inkjet printing accessory allows for the addition of vital product information, such as expiration dates and production lots, directly onto the packaging. This feature is crucial for traceability and compliance with labelling regulations.
Clean-In-Place System
The CIP (Clean-In-Place) system provides an efficient solution for cleaning the dosing unit. This independent system allows for the thorough sanitisation of critical components without disassembly, ensuring the machine remains hygienic with minimal downtime.
DETAILS
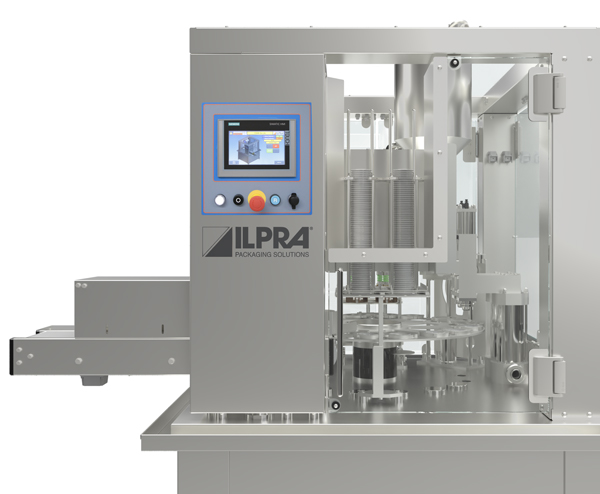
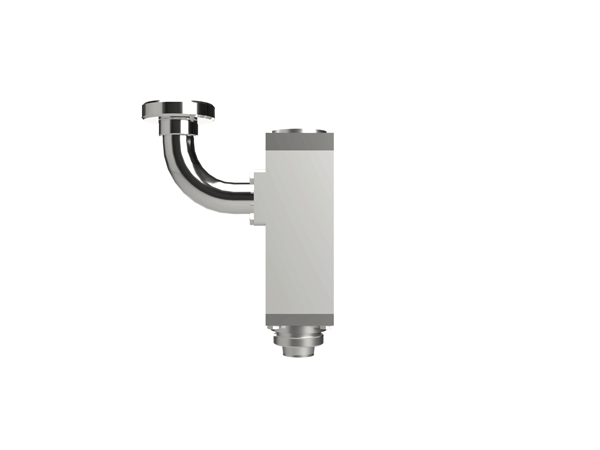
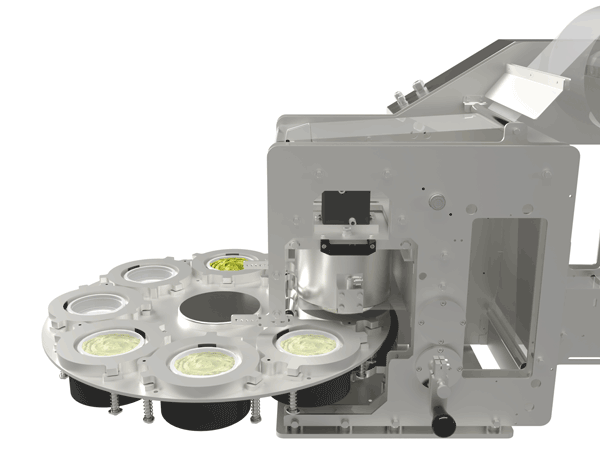
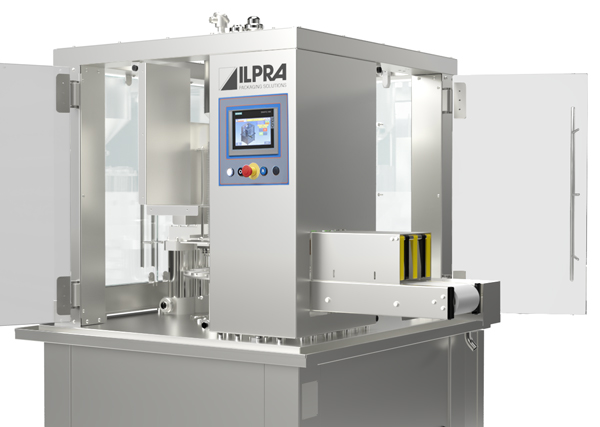
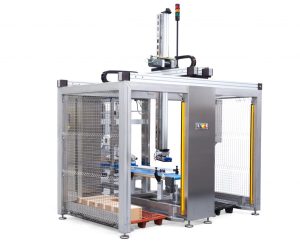
End of Line Add-Ons
Browse Compatible Machines
From palletizers to labellers, finalise your production line with automated packaging solutions.
Request a Quote
Get in touch here with our team to request a free quote. Our expert team will help you configure the best solution for your production line.
Get in touch
Speak to one of our experts
Get in touch with our team for tailored advice on which packaging solution is right for your products.